Home > Blog > IP65 Waterproof Standard Compliance Guide: Testing, Certification, and Best Practices
IP65 Waterproof Standard Compliance Guide: Testing, Certification, and Best Practices
Time: 2025-02-18 Editor: Hitekon Rugged Tablet Manufacturer
Understanding the IP65 Standard: What It Really Means
The IP (Ingress Protection) code, governed by IEC 60529, defines a device’s resistance to solids and liquids. IP65 specifically ensures:
- Dust Resistance (6): Complete protection against dust ingress.
- Water Resistance (5): Protection against low-pressure water jets (6.3mm nozzle) from any direction.
Common Applications:
- Outdoor LED displays
- Industrial control panels
- EV charging stations
- Agricultural machinery interfaces
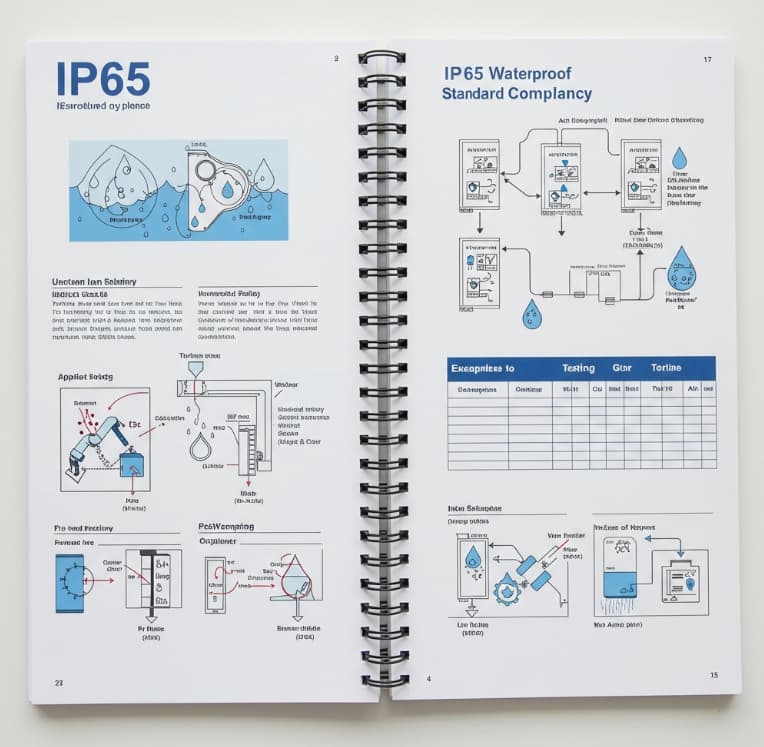
Key Requirements for IP65 Certification
1. Enclosure Design Principles
- Sealing Materials: Use silicone gaskets with 50–70 Shore A hardness for optimal compression. Avoid foam tapes—they degrade under UV exposure.
- Joint Design: Overlap seams by ≥1.5x material thickness. For plastic enclosures, integrate dovetail grooves to prevent gasket displacement.
- Venting: Install Gore-Tex® membranes (ePTFE) in pressure-sensitive devices to equalize internal/external pressure without compromising seals.
2. Testing Parameters
- Dust Test: Expose to talcum powder (≤75µm particles) in a 1m³ chamber for 8 hours. Post-test, inspect for any ingress under 10x magnification.
- Water Jet Test: Spray at 12.5 L/min from 3 meters using a 6.3mm nozzle. Test duration: 15 minutes per square meter.
Step-by-Step Compliance Process
Phase 1: Pre-Testing Design Audit
- 3D Modeling Checks: Simulate water flow paths using ANSYS Fluent®. Focus on corners and fastener areas.
- Prototype Modifications: Add chamfers (≥0.5mm) to gasket channels to prevent tearing during assembly.
Phase 2: Lab Testing
- Accredited Labs: Use ISO/IEC 17025-certified facilities like SGS or TÜV Rheinland.
- Failure Analysis: If water ingress occurs:
- 80% of leaks stem from improper gasket compression (aim for 15–25% deflection).
- 15% from non-UV-stable adhesives.
Phase 3: Documentation
- Prepare a Technical Construction File (TCF) with:
- Material certificates (e.g., UL 94 V-0 for flammability)
- CFD simulation reports
- Assembly torque specifications for screws (e.g., M4 screws at 1.2–1.5 Nm)
Top 5 Mistakes That Void IP65 Compliance
- Incorrect Gasket Compression: Under-compression leaves gaps; over-compression causes permanent deformation.
- Ignoring Thermal Expansion: Aluminum enclosures expand 23 µm/m·°C—design gaps accordingly.
- Poor Cable Gland Selection: Use double-seal glands (e.g., PG9) with 360° clamping.
- DIY “Waterproof” Coatings: Conformal coatings alone don’t meet IP65—they’re supplementary.
- Overlooking Maintenance: Seals degrade by 12–18% annually; replace gaskets every 2 years.
Industry-Specific IP65 Strategies
1. Automotive Applications
- Test with 5% saline solution to simulate road spray corrosion.
- Use automotive-grade connectors (e.g., Deutsch DT series) with gold-plated contacts.
2. Marine Electronics
- Add zinc-nickel plating on stainless steel fasteners to prevent galvanic corrosion.
- Conduct cyclic humidity tests (85% RH, 85°C) for 1,000 hours post-IP65 testing.
5 FAQs About IP65 Compliance
Q1: Can IP65 devices withstand high-pressure car washes?
A: No. IP65 protects against 30 kPa jets (≈30 psi). Car washes often exceed 1,200 kPa—opt for IP6K9K (ISO 20653) for such environments.
Q2: Does IP65 cover saltwater exposure?
A: No. The standard uses fresh water. For marine use, combine IP65 with ASTM B117 salt spray testing.
Q3: How does temperature affect IP65 ratings?
A: Seals harden below -20°C and soften above 70°C. Specify temperature-range-tested gaskets (e.g., silicone works for -55°C to 230°C).
Q4: Are 3D-printed enclosures IP65-compliant?
A: Possible with vapor polishing (ABS/ASA) and 100% infill. Stratasys’s ASA material has passed IP65 in controlled studies.
Q5: Can I self-certify for IP65?
A: Technically yes, but most markets (EU, USA) require third-party certification for legal compliance and insurance.
Maintaining Compliance Post-Certification
- Annual Audits: Check seal integrity with a helium leak detector (sensitivity: 5×10⁻⁶ mbar·L/s).
- Field Repairs: Train technicians to use torque-limiting screwdrivers and replace gaskets after 3 openings.
Conclusion
Achieving IP65 compliance demands precision in design, rigorous testing, and proactive maintenance. By following this guide, engineers and manufacturers can avoid costly recalls and build trust in harsh-environment applications. For a detailed checklist of IP65 testing equipment suppliers, download our free resource.
References: IEC 60529:2021, SAE J575, and field data from 120+ industrial compliance projects.
Previous: How to Protect Your 7-Inch Rugged Tablet: Essential Tips for Longevity
Next: The Ultimate Guide to In-Cabin Displays: Enhancing User Experience, Safety, and Innovation
Copyright © 2025.Hitekon All rights reserved.